Thanks for the quick response. After performing some checks, I found that there wasn’t any voltage differential between the RED/BLK pins on the HX711 board. After replacing the wire from the Arduino to the CLK pin, it started working. However, after getting numbers printing out, I noticed that there is some rather significant drift (see attached graph) and the readings are sinusoidal. What could be causing this?
The pins between the HX711 board and Arduino are as follows:
VDD/BCC → 5v
DAT → A3
CLK → A2
GND → Gnd
I am using the SparkFun_HX711_Calibration code with the only modification being to the DAT and CLK pins.
#include “HX711.h” //This library can be obtained here http://librarymanager/All#Avia_HX711
#define LOADCELL_DOUT_PIN A3
#define LOADCELL_SCK_PIN A2
HX711 scale;
float calibration_factor = -7050; //-7050 worked for my 440lb max scale setup
void setup() {
Serial.begin(9600);
Serial.println(“HX711 calibration sketch”);
Serial.println(“Remove all weight from scale”);
Serial.println(“After readings begin, place known weight on scale”);
Serial.println(“Press + or a to increase calibration factor”);
Serial.println(“Press - or z to decrease calibration factor”);
scale.begin(LOADCELL_DOUT_PIN, LOADCELL_SCK_PIN);
scale.set_scale();
scale.tare(); //Reset the scale to 0
long zero_factor = scale.read_average(); //Get a baseline reading
Serial.print("Zero factor: "); //This can be used to remove the need to tare the scale. Useful in permanent scale projects.
Serial.println(zero_factor);
}
void loop() {
scale.set_scale(calibration_factor); //Adjust to this calibration factor
Serial.print("Reading: ");
Serial.print(scale.get_units(), 1);
Serial.print(" lbs"); //Change this to kg and re-adjust the calibration factor if you follow SI units like a sane person
Serial.print(" calibration_factor: ");
Serial.print(calibration_factor);
Serial.println();
if(Serial.available())
{
char temp = Serial.read();
if(temp == ‘+’ || temp == ‘a’)
calibration_factor += 10;
else if(temp == ‘-’ || temp == ‘z’)
calibration_factor -= 10;
}
}
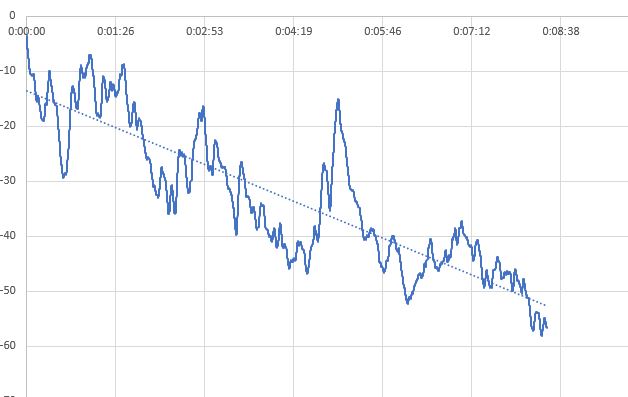