Hi, i’m trying to build an automatic pouring machine. User chooses a maximum weight of a fluid, then he puts a bottle on the scale, and press a button. The machine keeps a valve open until the weght on the scale matches the chosen one. To build the scale, im using 4 50kg strain gauges, a sparkfun load sensors combinator, and a sparkfun HX711 amplifier, and here are the problems. Scale is giving me very unstable readings. When everything is mounted, the differences between reading is up to 2kg. And thats not all but i think problems have same source. Here’s more of this. When the wires were laying free on the floor, i could change the reading simply by moving one of the strain gauge wire. Now i did cable management but even a simple vibration affects reading. I saw some videos on YouTube and people gets readings stable up to second decimal point.
I tested second set of parts (bought everything new) but i still have this problem. I hook up everything using your hook-up guid and i run calibration program from that website. Thanks in advance, and sorry for my english, i hope you understood me well
Make sure your wiring is correct vs the hookup guide(s), and that the wires are of equal length with solid soldering connections.
A 2kg difference in reading if it’s at max load (200kg? mentioned 4x 50kg) might be expected
I’m sure the connections are right because I’ve been struggling with it for week until I posted here so I checked everything many times. 2kg and sometimes even bigger jumps are happening all the time even without any weight on the scale and after the tare() function. What do you mean with equal wires length? I didn’t cut the original strain gauges wires and I think they have pretty the same length. Although in my setup some of them are bended and some of them are going straight. (Strain gauges are in different distances from hx711 looking in pairs)
And first of all thanks for reply
You will benefit from using averaging of readings; but the jumps you are depicting indicates as @TS-Russell indicated something amiss with your connections. I am not an expert in load cellls but I do know that when using a wheatstone bridge the inputs need to balance out. Things that come to mind: what are the strain gauges you are using (SFE’s load combiner only works with some types), are the connections to the strain gauges and the load combiner soldered.
Everything is soldered, and about averaging, i made a program that takes 20 readings (I didn’t use the read_average() function instead made it myself) then takes average and then rounds it to nearest 0.5 and it didn’t help. I can get few stable results in a row but nothing improved in a long term. I will try to combine strain gauges by myself, maybe it will be better
How about the gauges themselves; which type are you using?
I can’t paste the link here maybe it will work on pc, but they are this three wire strain gauges with 2k resistance in total and 1k from plus or minus to combinator wire. Combining them by myself didn’t work
Can you send photos of the back of your boards and a photo showing the general setup? Another photo showing how the load cells are mounted would be helpful too.
Yesterday after the tests I reassembled my setup, but it was a piece of wooden board and the strain gauges were mounted with insolation tape. Here are photos of my boards. Now I’m using my one board for combination but it has the same connections as the sparkfun combination board. And taking about the hx 711 board I added a capacitor between gnd and vcc to filter supply noise but it didn’t help. I also connected the B channel to ground because I was thinkin that it’s collecting noise from environment but it didn’t make any difference. However in some versions of hx711 this channel was connected originally to ground so I thought it may help. And last think is that I closed the gap to set the rate to 10 SPS, but later when I checked with multimeter It was already connected to ground (which mean 10 SPS even without my soldering). Of course all of this didn’t help. Here are photos.
1- Don’t know why you have B+/B- connected to ground, I would not do that.
2- Can’t see how you have the sensors wired, but it looks like this and if so, that’s correct.
https://i.stack.imgur.com/9vDyI.jpg
3- The way you mount the sensors matters, have a look at this post:
viewtopic.php?f=79&t=50303&p=205638&hil … rs#p205638
I will check again but I think the sensors are connected as you showed, I can disconnect channel b from ground but connecting it didn’t make difference. I will look at proper mounting sensors when I will be back in home after work, thank you for idea
Ok I had some time to look at it fast, and my sensors were mounted wrong, I didn’t have any space for the moving part. I will get proper setup and test it again. But I wonder why did this affect reading in the way it did, and will it solve the problem with moving wires causing noise
Man you are awesome YellowDog i love you so much. Scale works perfectly and its all thanks to you. i would never think of this. I spent more than two weeks trying to figure it out and you solved my problem. Thanks you from all of my hart (we say that in poland idk if it makes sense in english) i love you.
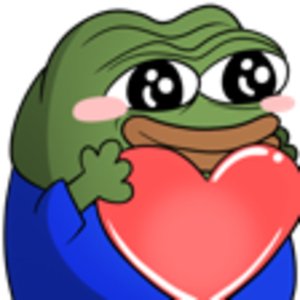
I’m very glad I could help! 